Technical Direction
of
RIDE THE CYCLONE
Book and Lyrics By
Jacob Richmond and Brooke Maxwell
Director: Ryan Scoble
Scenic Designer: Jess Ford
Lighting Designer: Maren Taylor
Sound Designer: Alan McEwen
Costume Designer: Emmalee Berger
Projection Designer: Jada Pinsley
Stage Manager: Rachel Rock
Technical Director: Pat LoRicco
Riding the Cyclone: Mastering Technical Theatre
Ride the Cyclone is an absolute emotional rollercoaster of a show. This is an amazing story about five teenagers on the precipice of their lives who die in a freak carnival ride accident and must share their life's greatest hopes for a second chance at life. I am so fortunate that this show was chosen as my thesis project at West Virginia University. This production was not only one of the best shows I have been a part of at WVU but was also one of the largest and most technically complex I have done to date. That being said, for me, this project started back in April with the final designs.
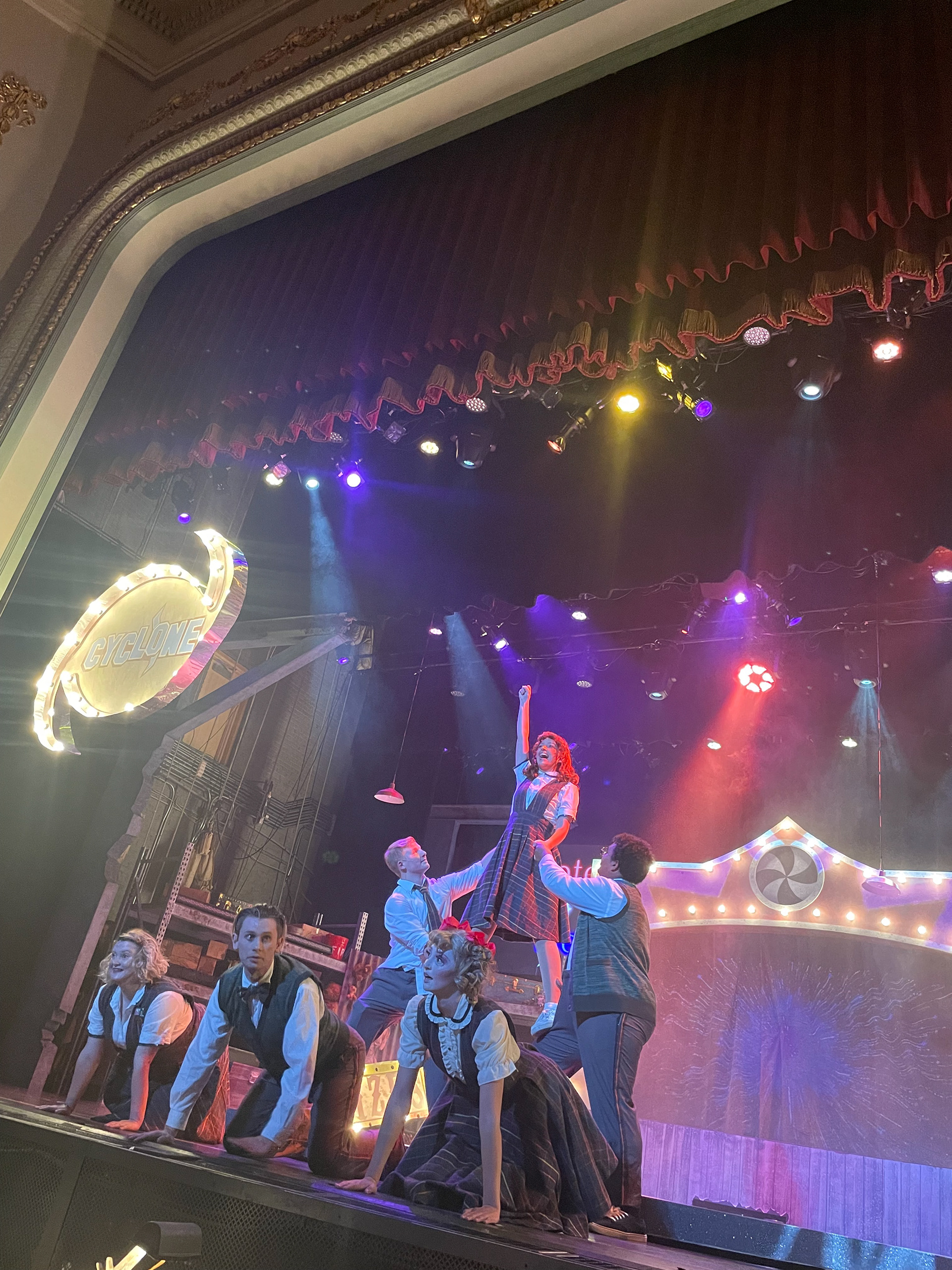
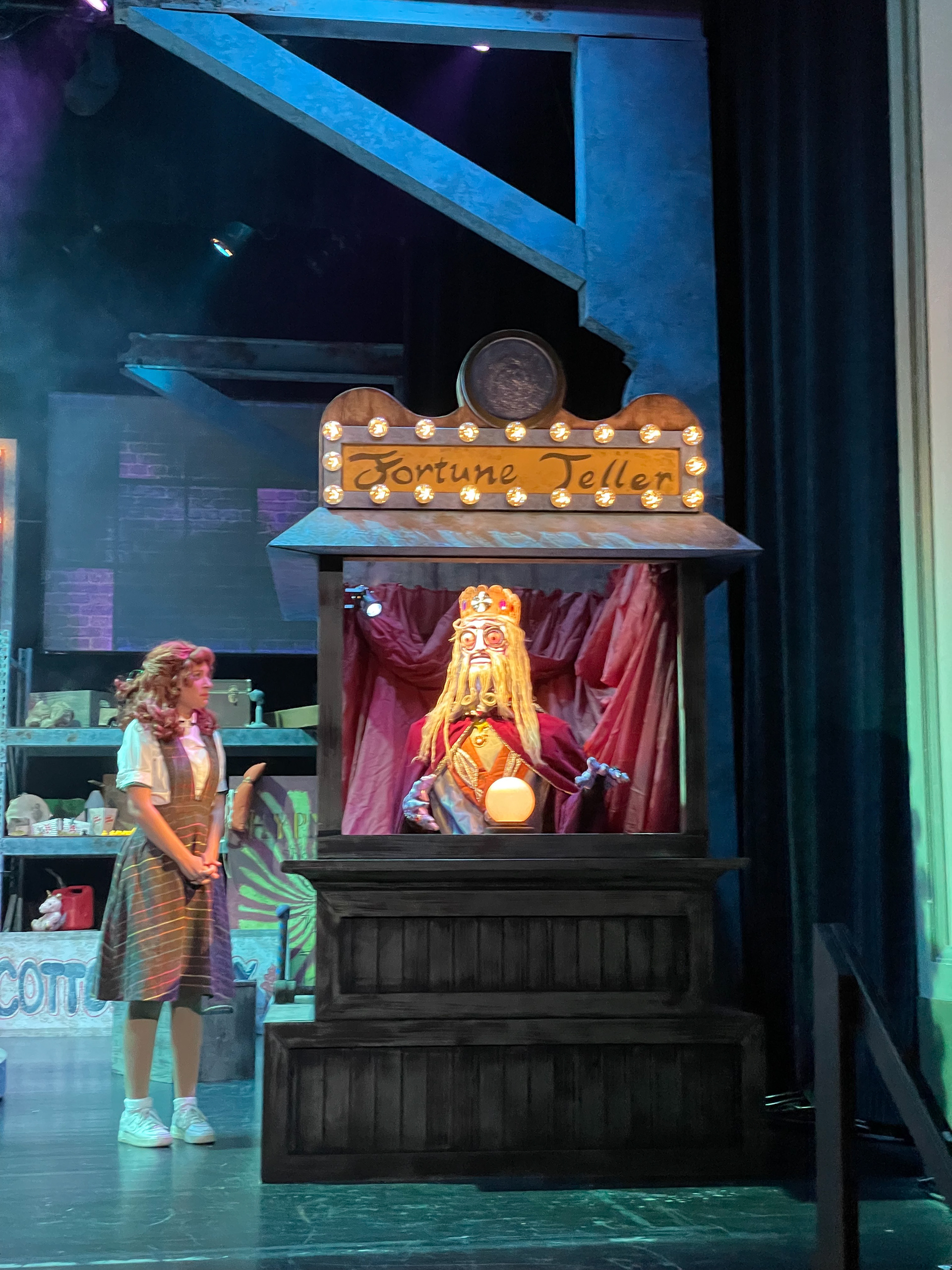
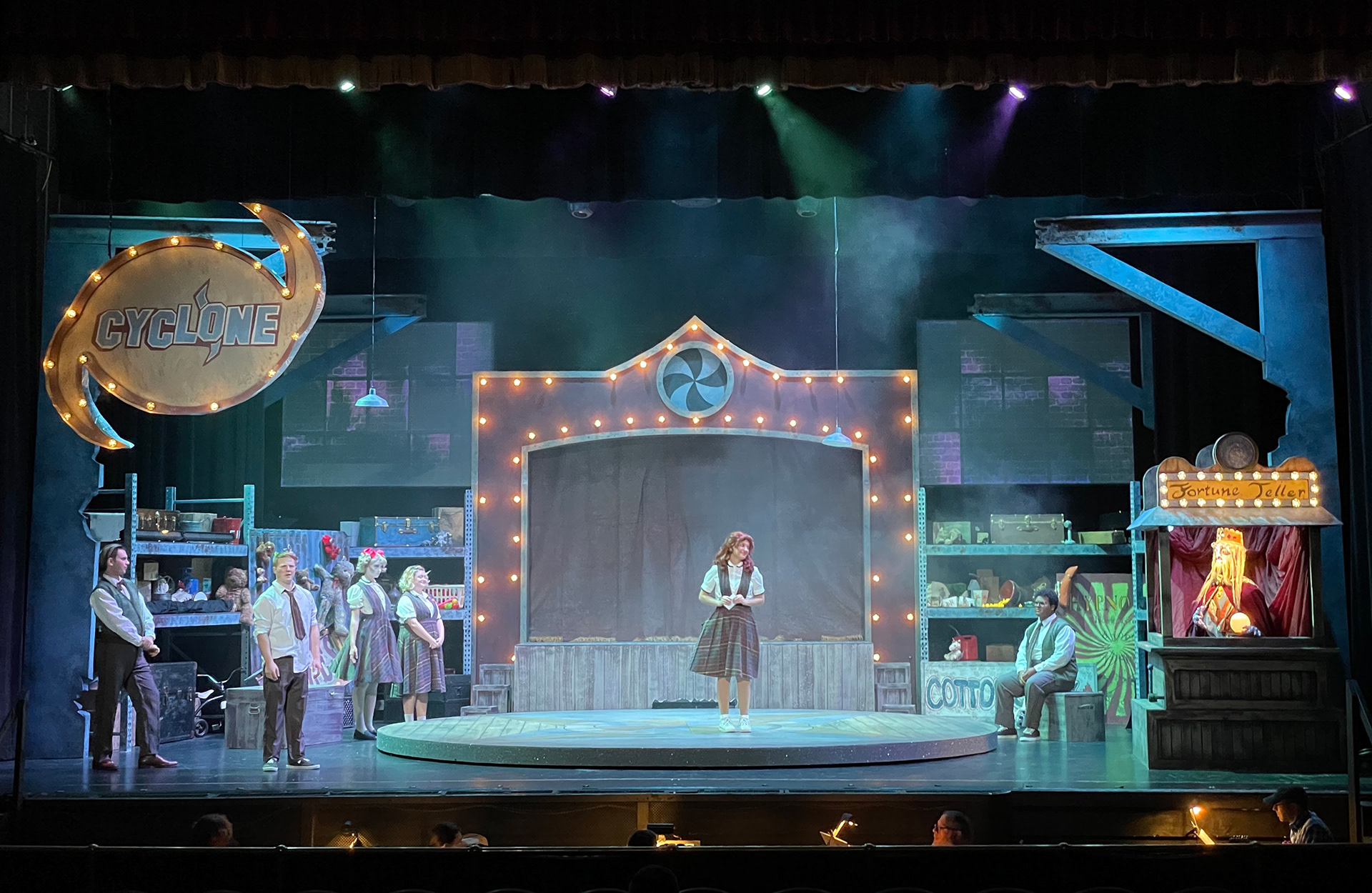
Inside the Warehouse
This show takes place in an abandoned warehouse-turned-purgatory full of hastily leftover carnival equipment. Stuffed prizes, signs, and popcorn containers are scattered amongst the old rides and booths left behind. Among the storage, Karnak, the animatronic fortune teller becomes the narrator and the guide for the teenagers in their transition. The design included a small proscenium arch and stage with a working tableau curtain, concrete beams with rusting I-beams, and warehouse windows with rear projector screens. Several industrial shelves, lit signs, and crates are scattered around the central turntable/ carousel base. The total scenic budget for this show was $5500, with 475 labor hours for build and 200 hours for load-in. The set would also need to be transported from our shop to the historic Metropolitan Theatre in downtown Morgantown
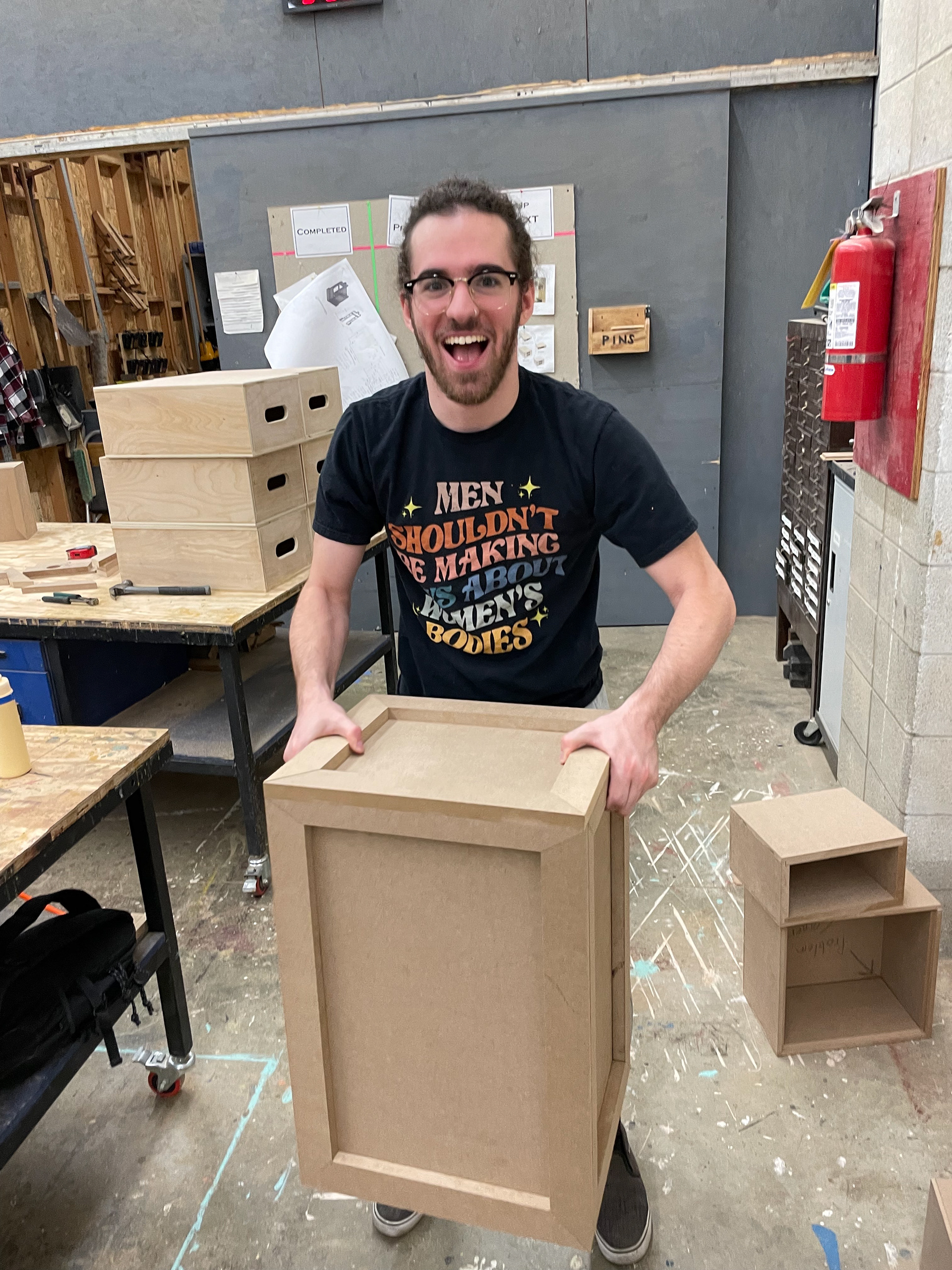
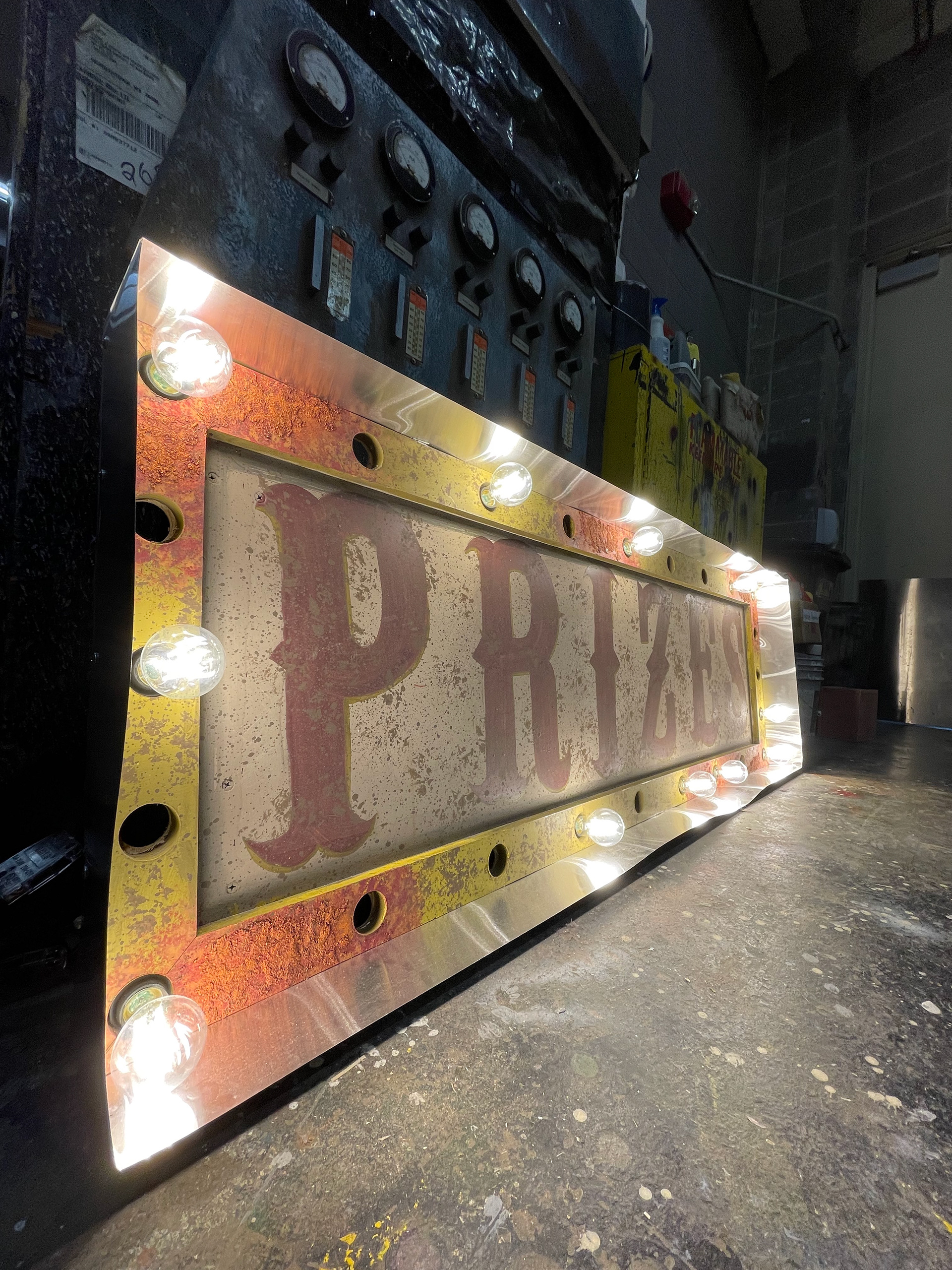
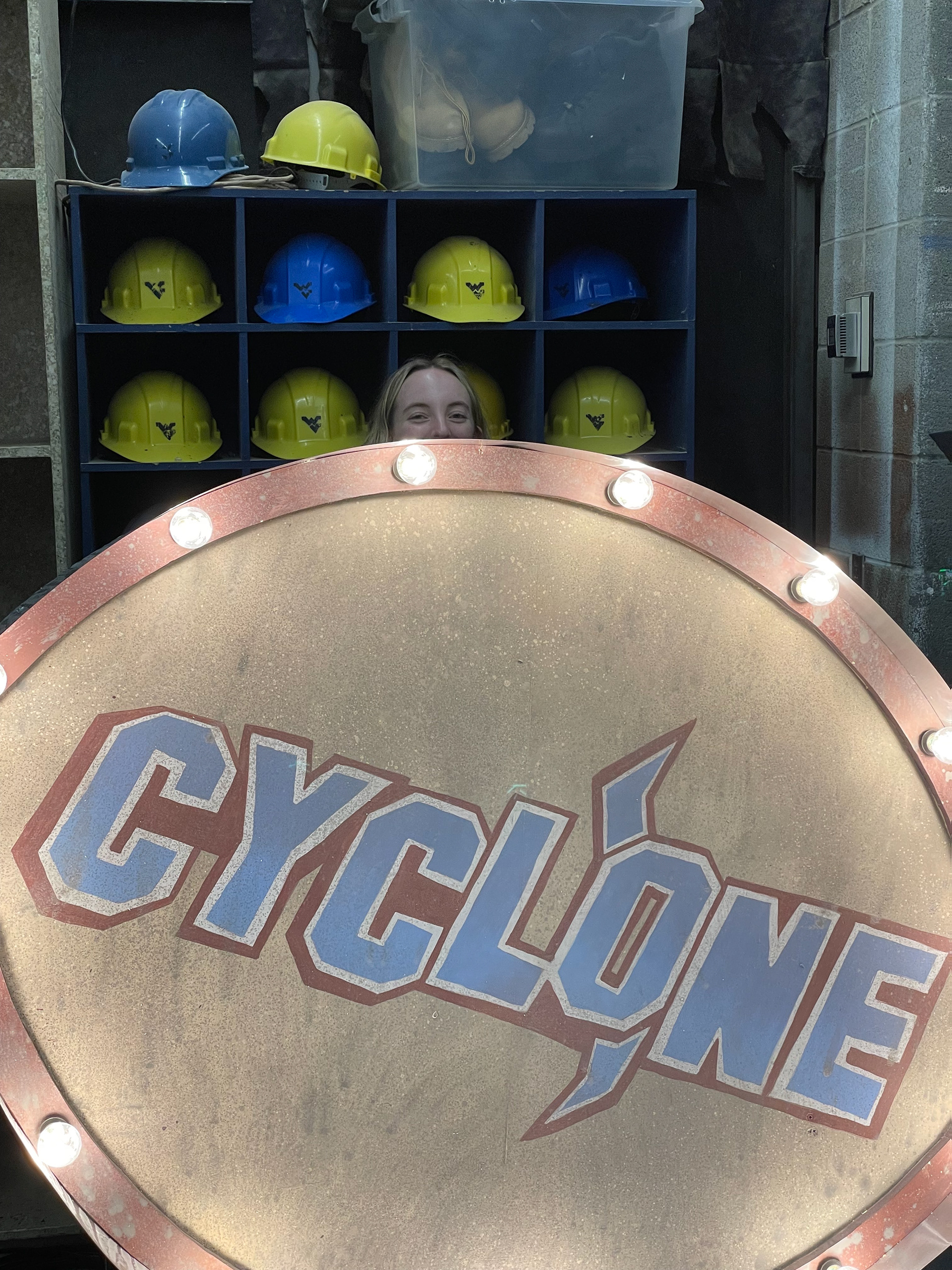
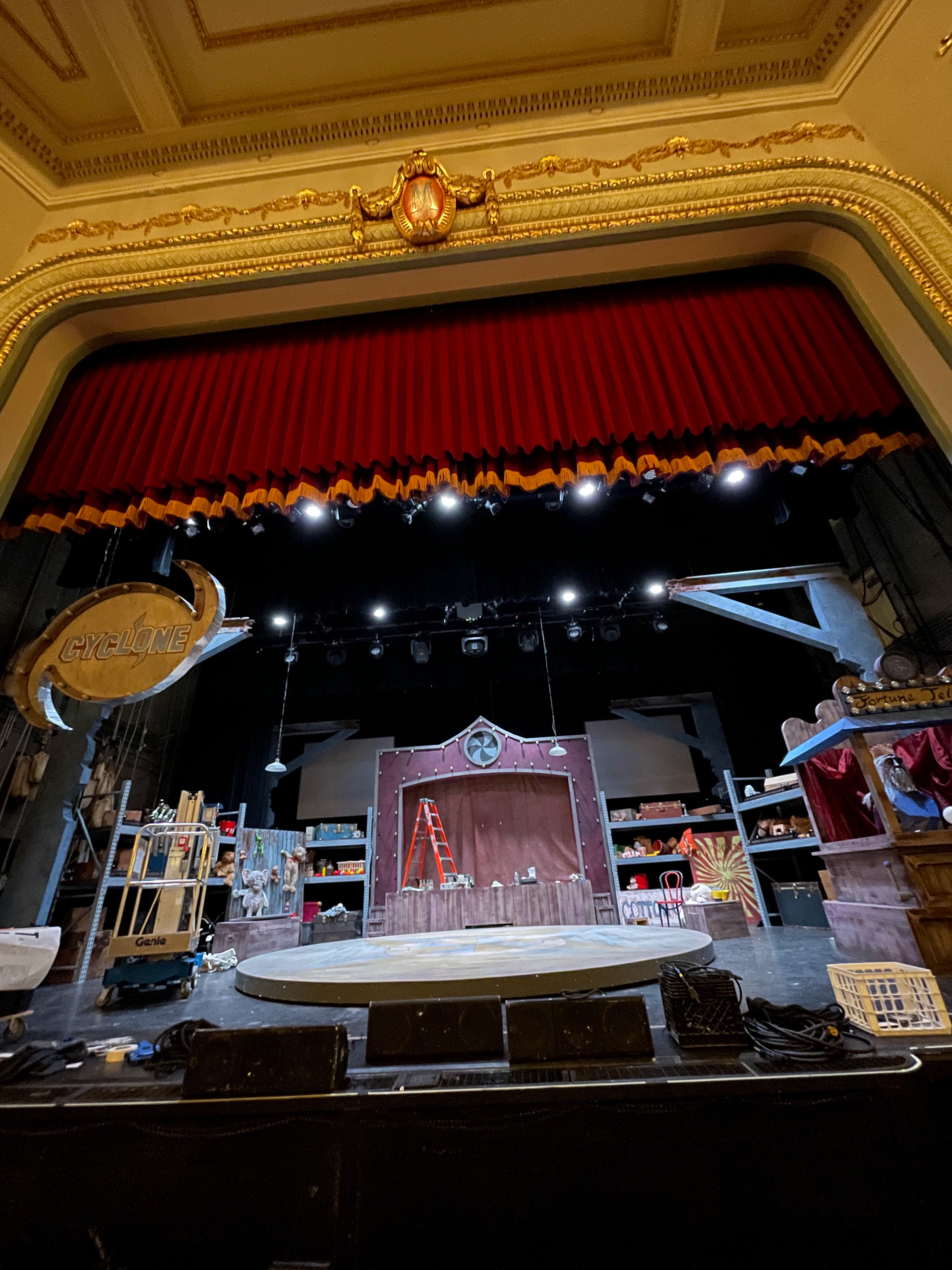
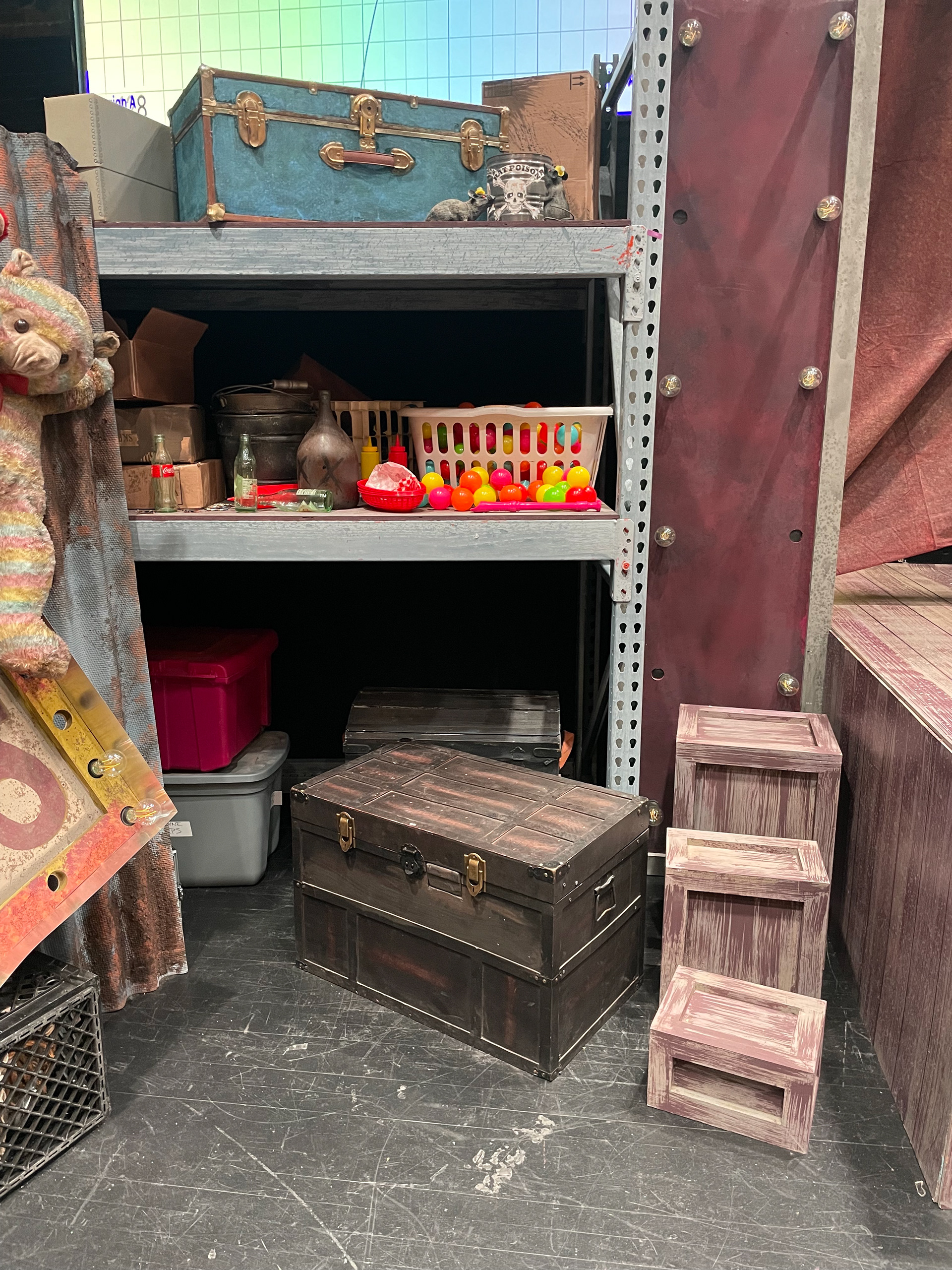
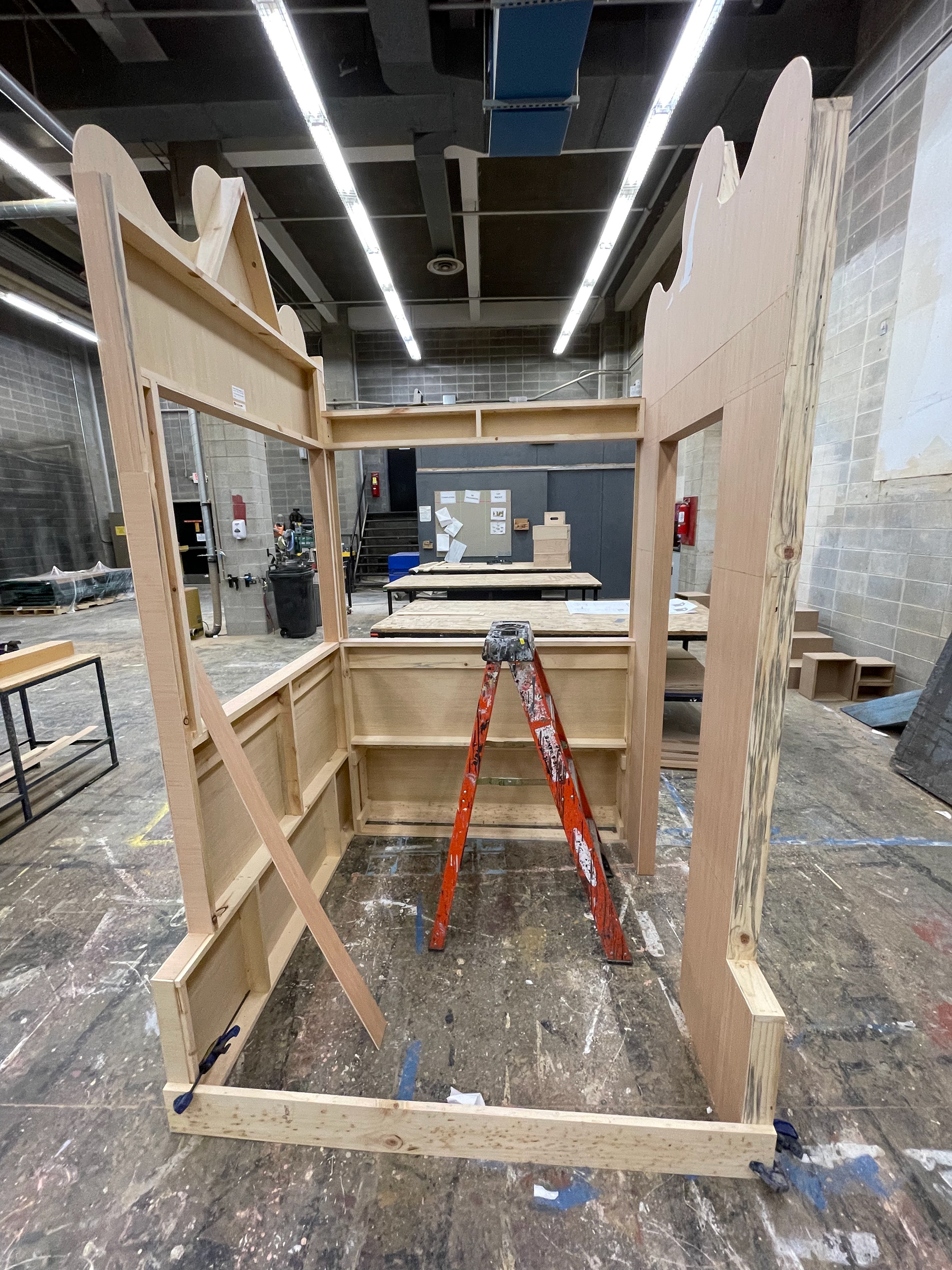
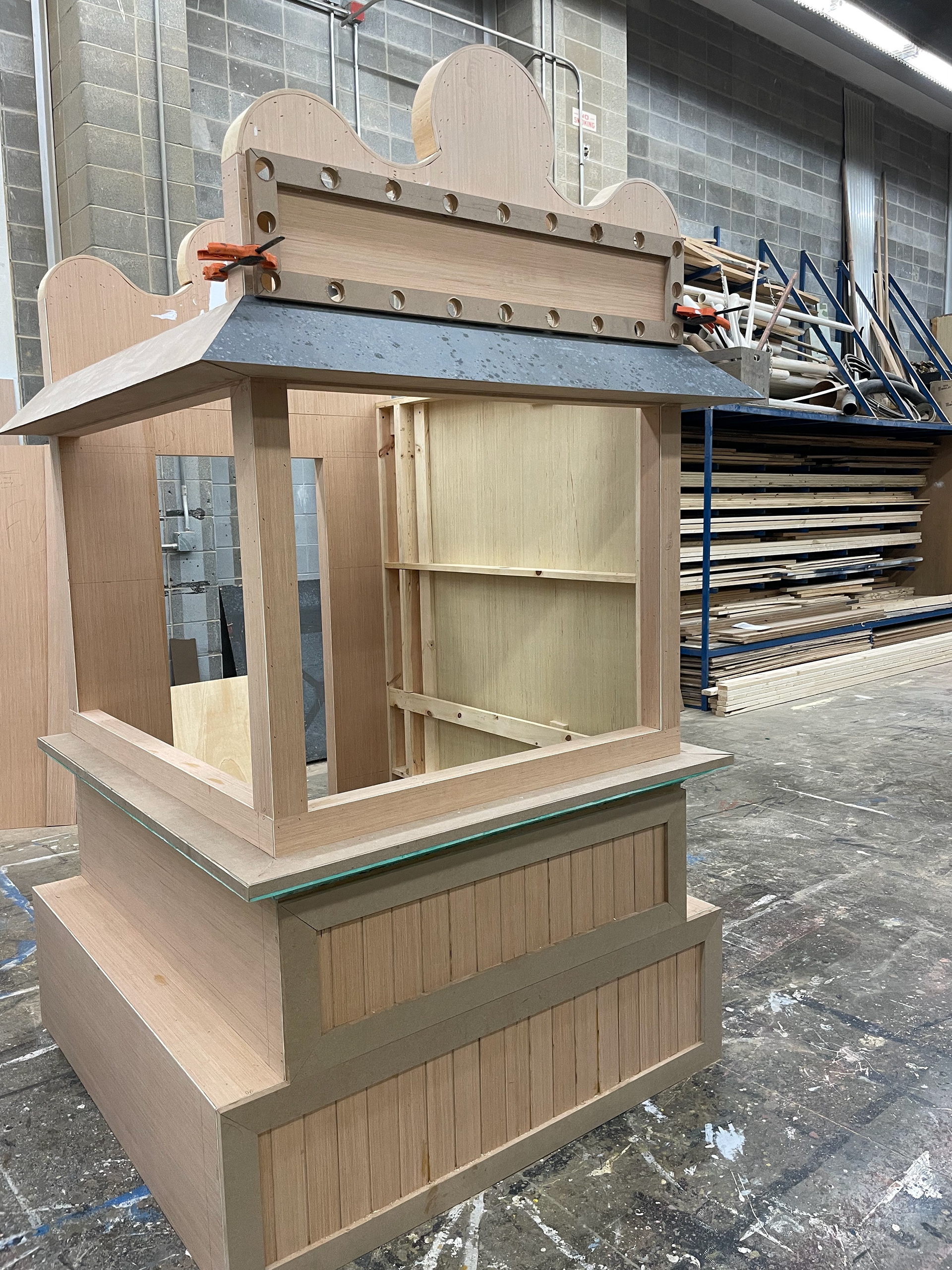
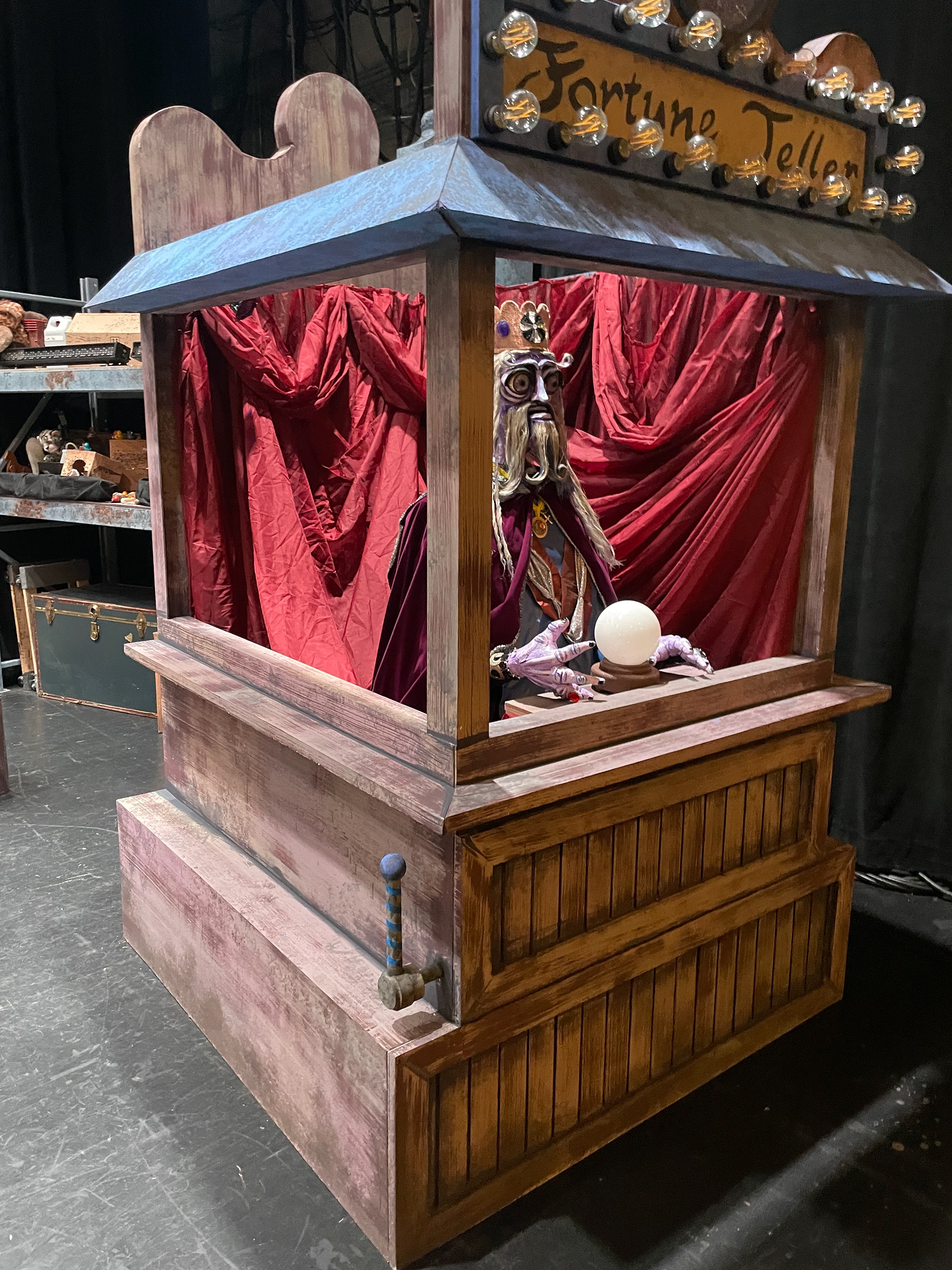
Crafting the Karnak Booth
The booth that would hold “the Amazing Karnak”, who was controlled by two fantastic puppeteer students, was mainly built using five Hollywood-style flats. I made sure to draft this unit in 3D to make sure all of the pieces would properly fit together. The unit had large custom trim work and a wood plank facade, as well as a sign surrounded by working lights, a crystal ball table, and a working spring-loaded crank to initiate the fortune telling. This unit was designed to disassemble into five separate pieces for easy transport to the Met and fast assembly during load-in.
Breaking Down the Portals
Two things that I relish as a technical director are to recycle material, and to add my own bits of creativity into a design when I am able: I got to do both with the “portals” or the warehouse beams. The beams were originally built for our production of Brightstar. We marked and cut out sections to give a weathered appearance. I reinforced the steel framing to keep the structure intact. We added layers of polystyrene foam to the cutouts to give the illusion of being solid concrete. We custom build I-Beams with ¾” MDF attached to steel framing that would be rigged to battens to keep them upright. On the ends of the beams, I cut out sections using a rotary saw and and jigsaw. I think using different diameter drill bits to puncture the beams with holes really made the corrosion look more realistic. Once the paint detail was added, they looked exactly like rusted steel. This was one of my favorite little details in the design.
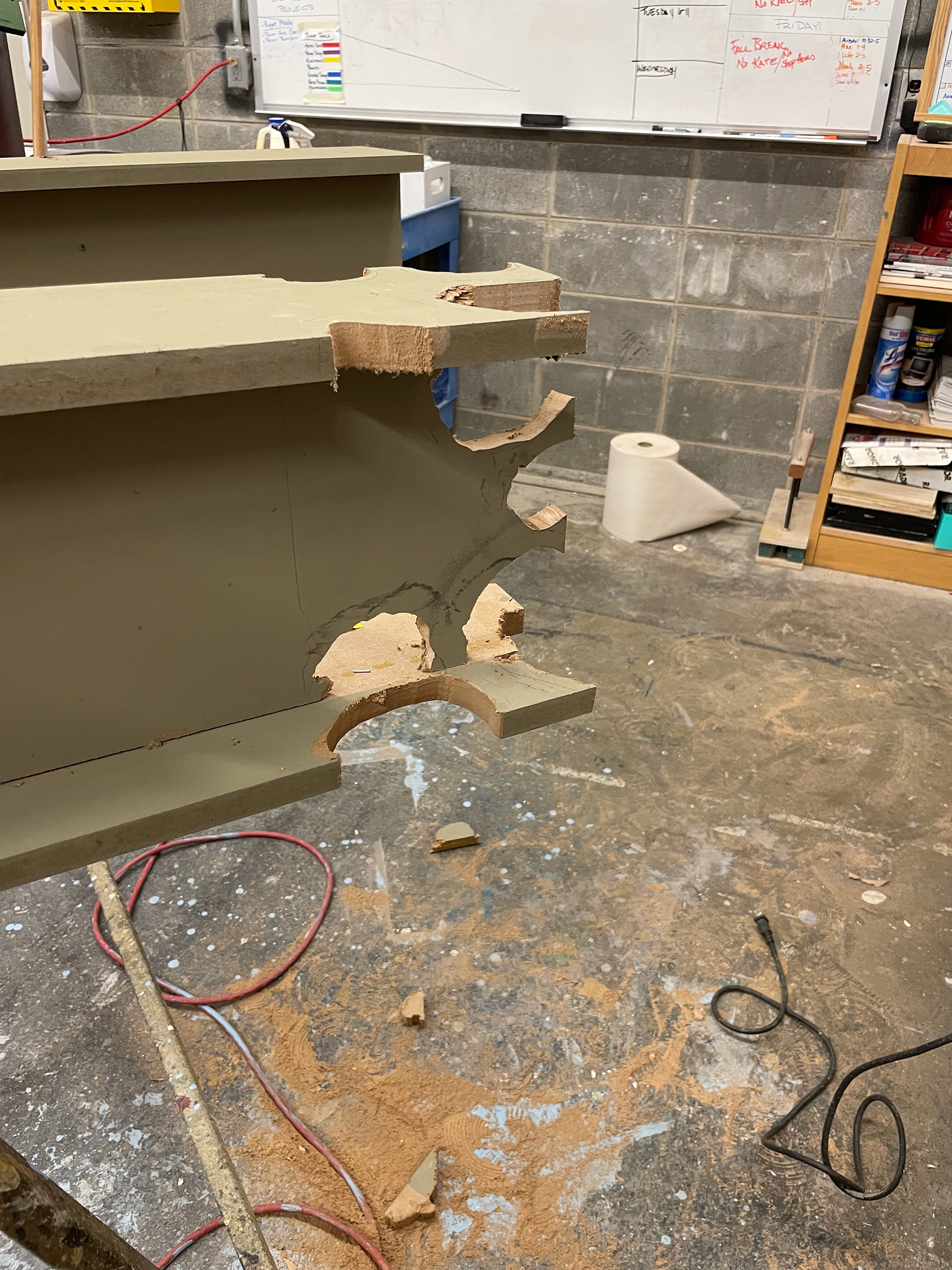
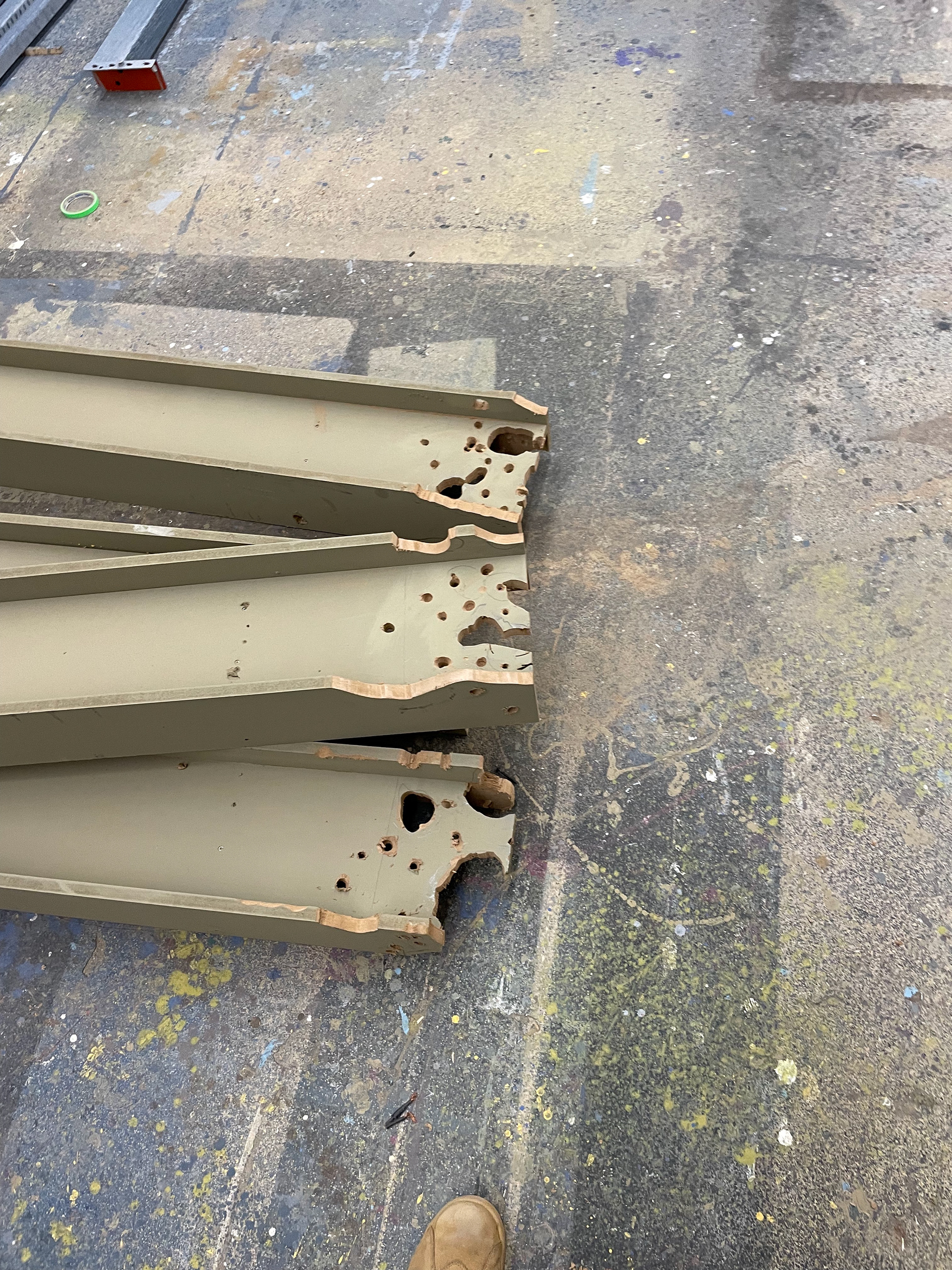
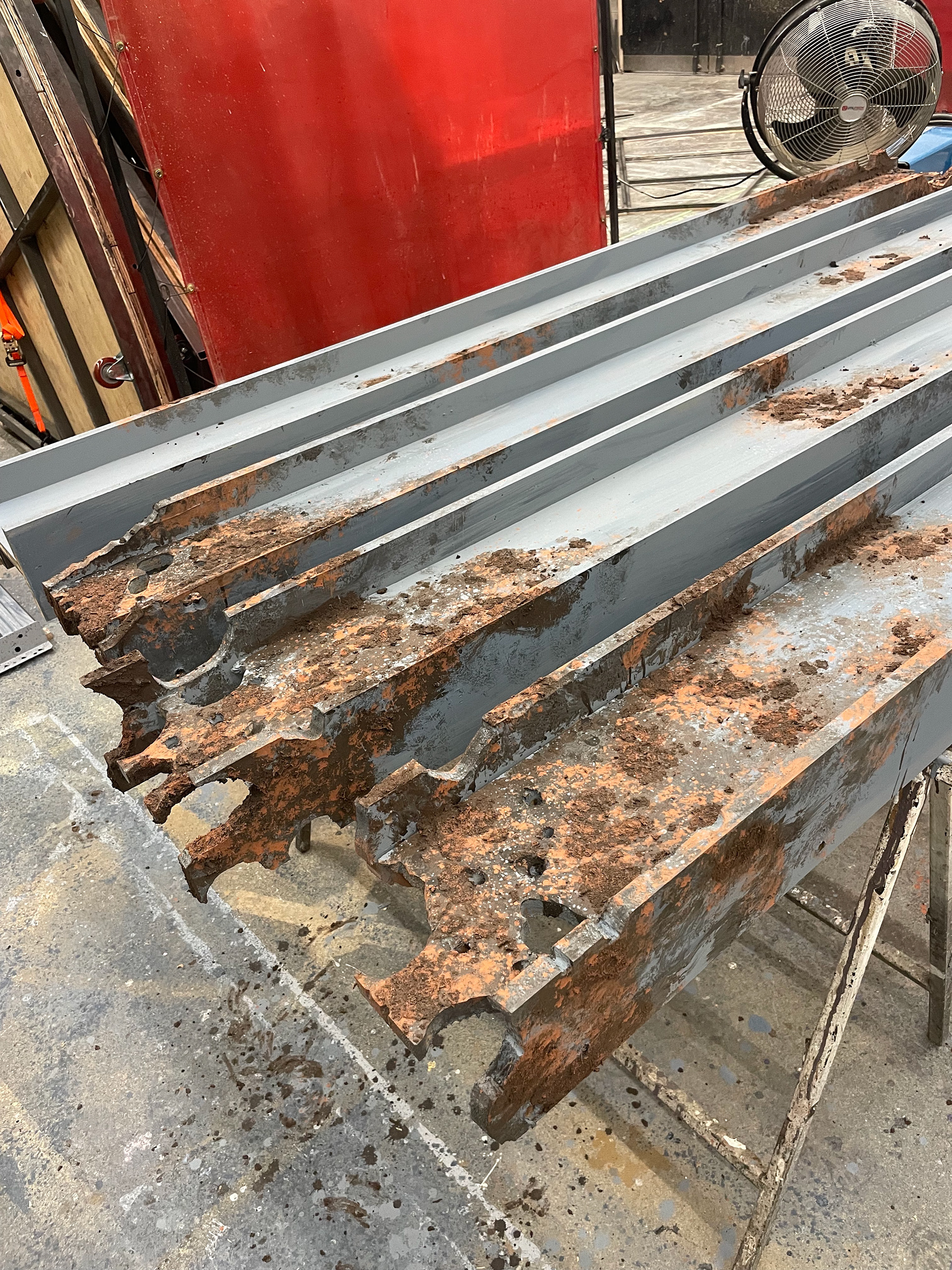
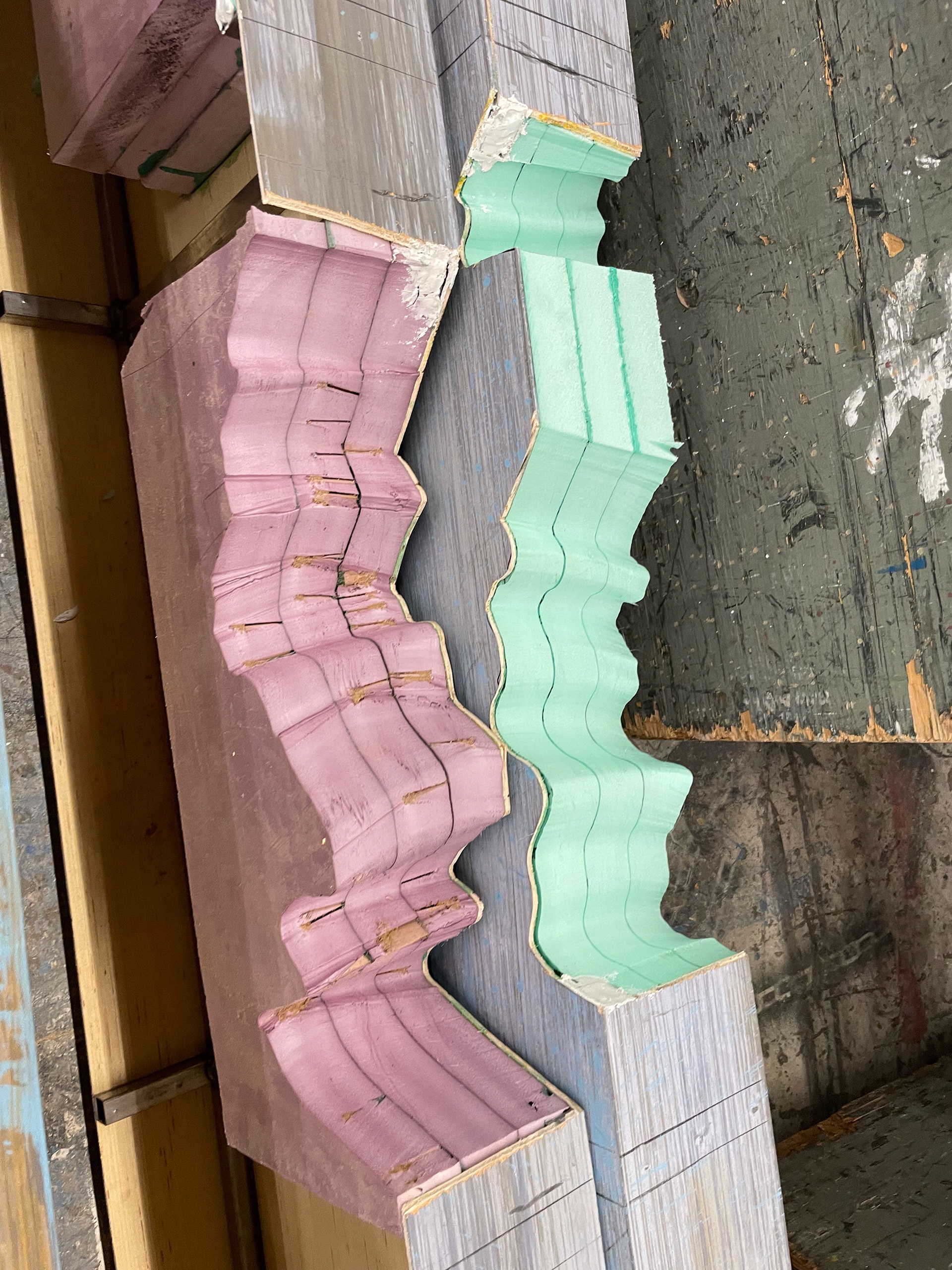
Steel Construction: The Proscenium Arch
Before I started grad school, I had only done welding on one show, many years ago. Now, I do some form of metalwork on every show, and I love it. I chose to make the small proscenium arch out of steel so that it could span the 12’ stage without drooping or needing extra support, especially with the weight of the curtain. I also wanted to build the unit in three pieces so I would be able to transport and assemble it easily while making it durable enough to last the trip. I started by cutting the luan facing and built the frame to fit. This ensures a perfect fit once you assemble everything, I used luan along the sides to give it depth and added ¾ MDF trim.
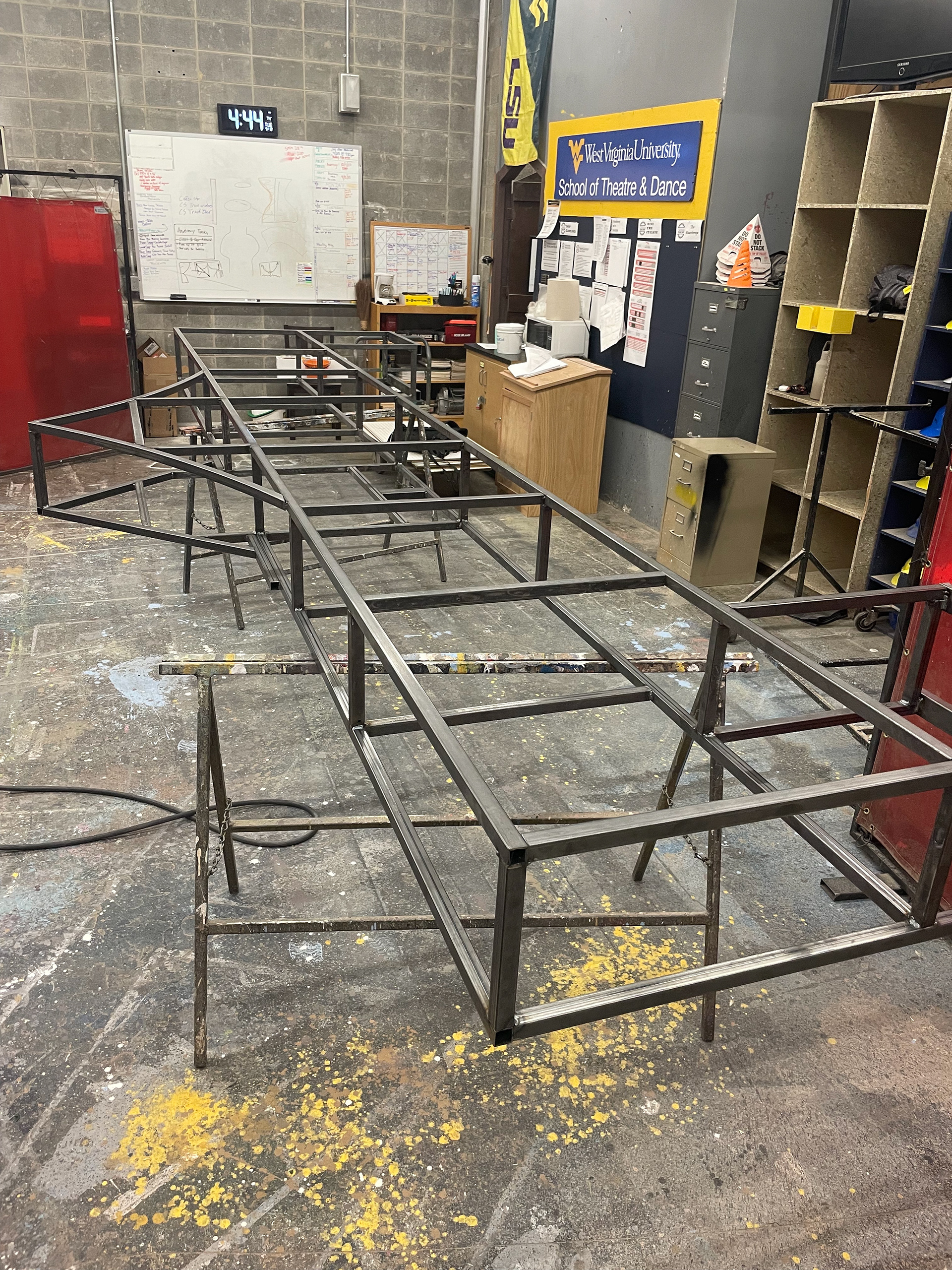
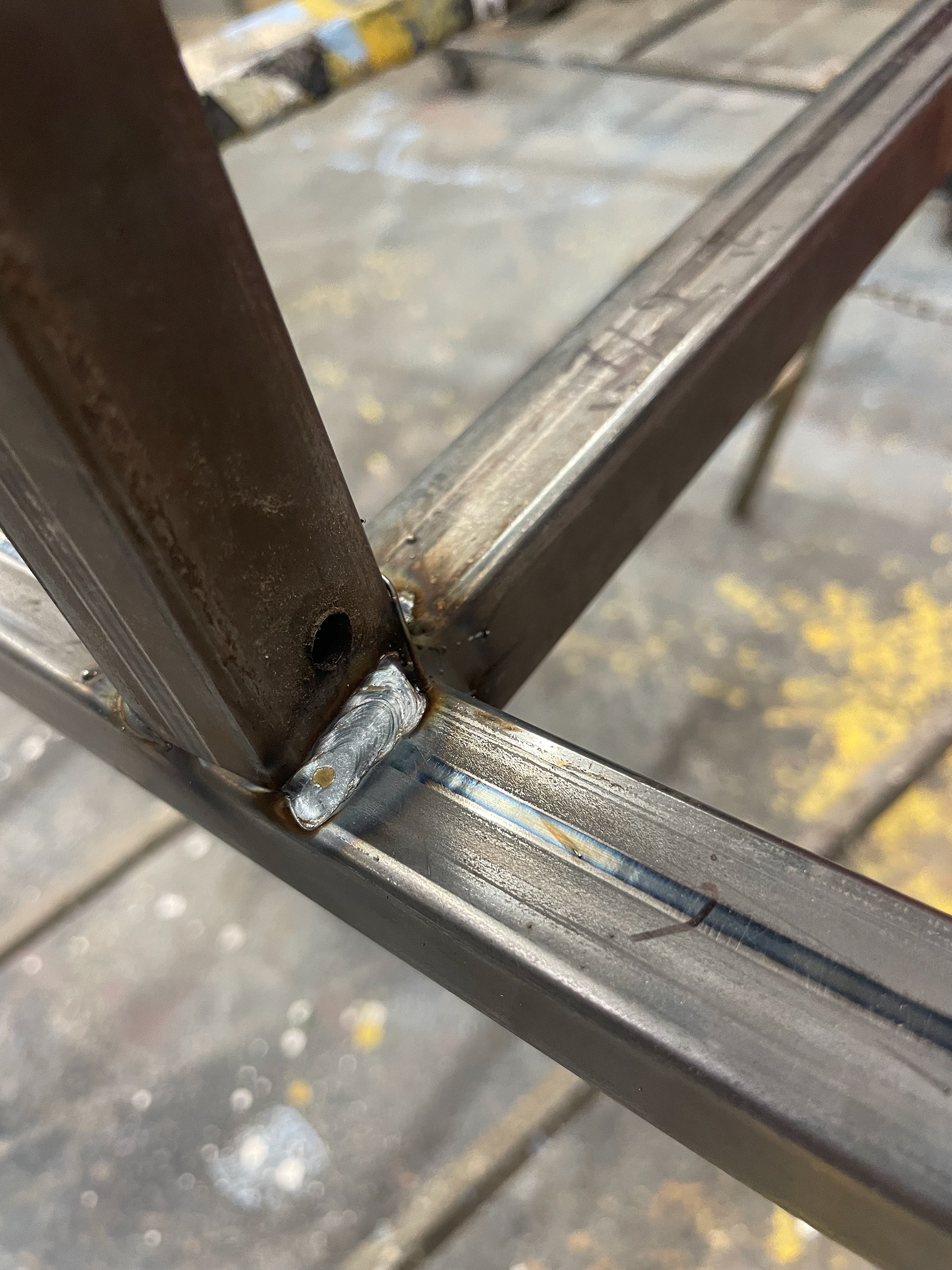
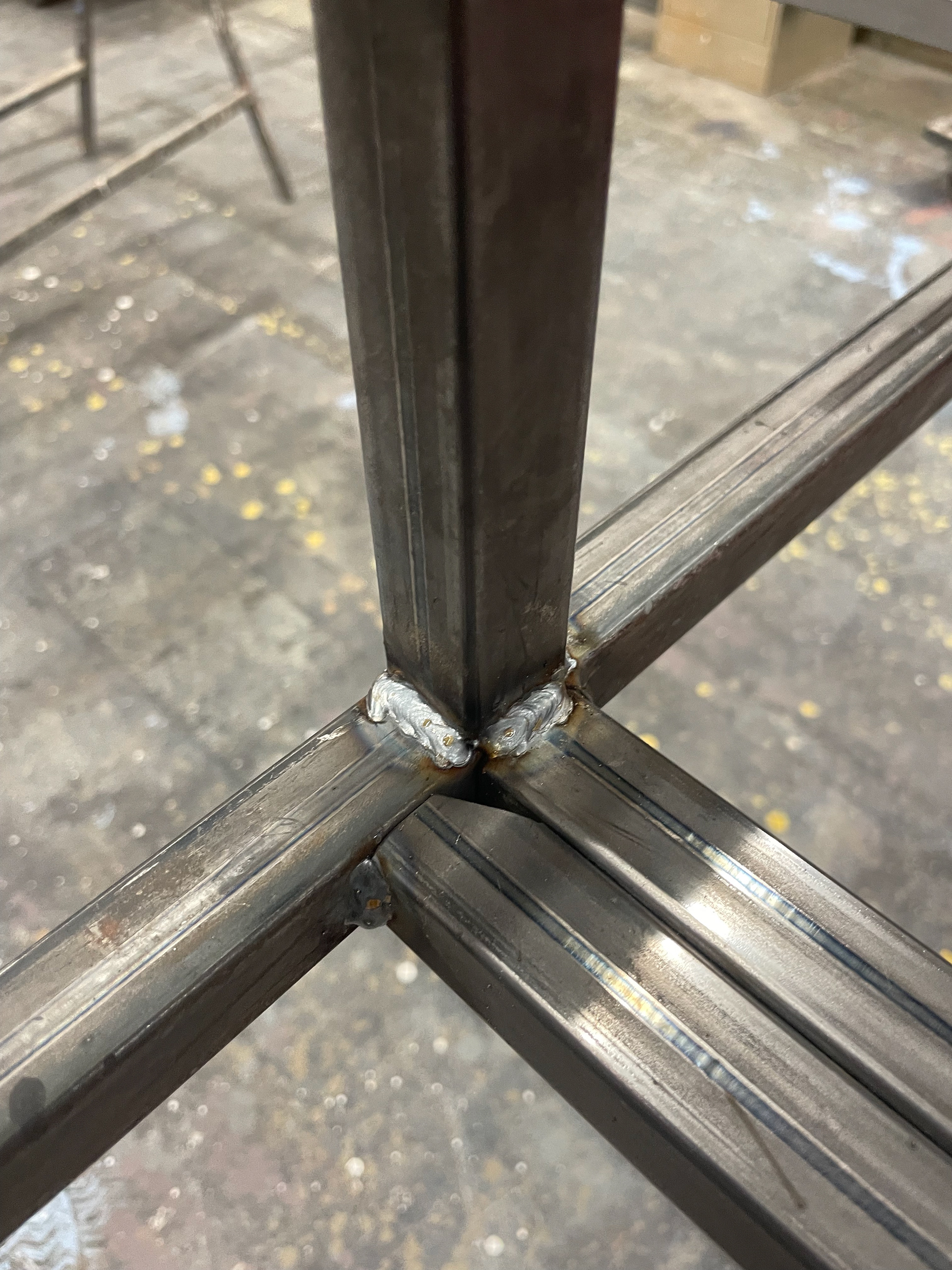
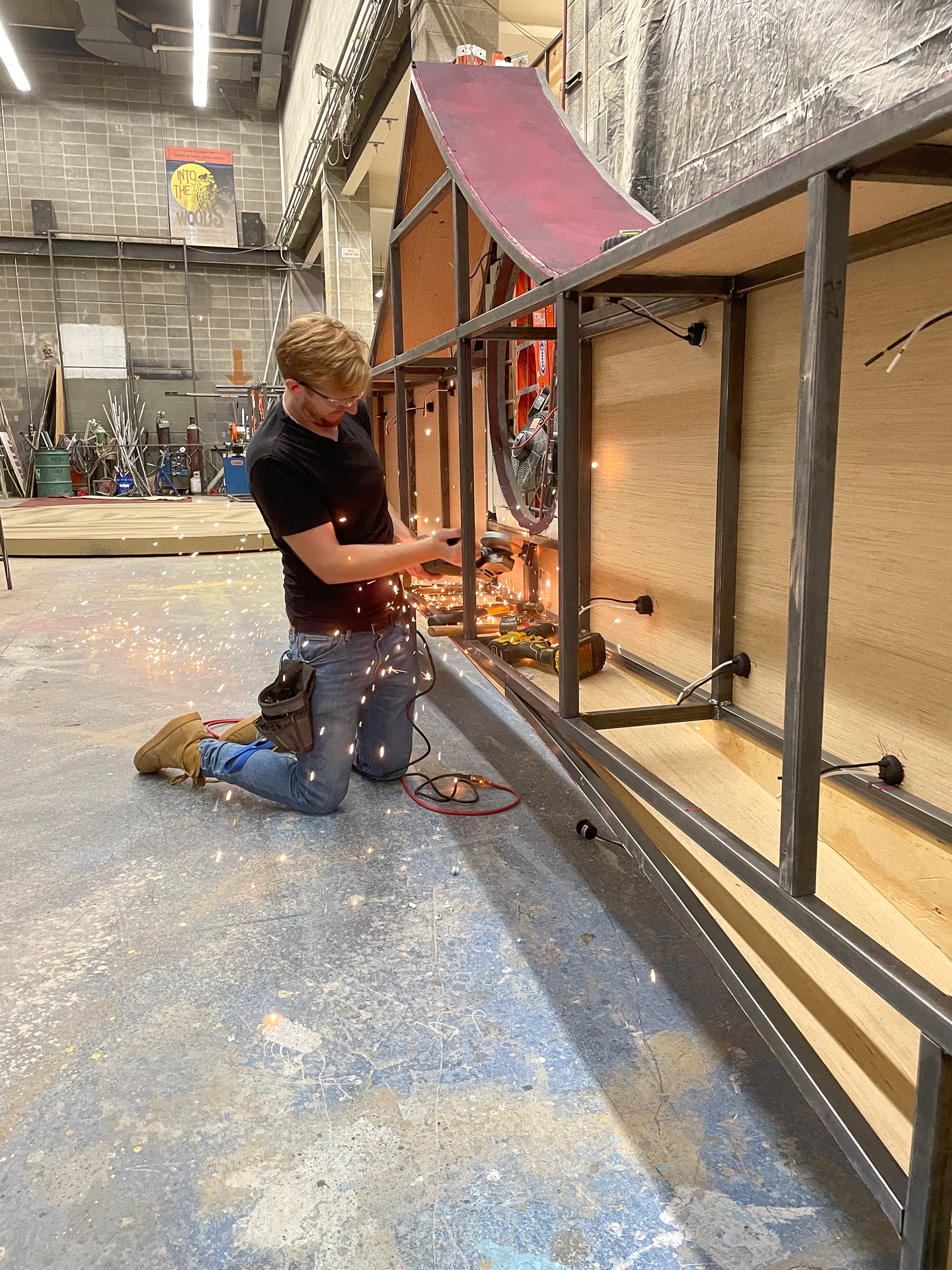
The curtain is tied to the proscenium with tie line, and uses 1/16 wire rope running through a series of rings sewn into the curtain that runs through several sheaves mounted to the frame to a single operating line off stage. We fine-turned the effect by adding an extra trim chain to the onstage edges of the curtain so it would close consistently. There was something about the swiftness of the direct operating line and the way the effect was run that almost gave the curtain its own personality in the show.
Here is a day in the shop building Ride the Cyclone!
Pulling All the Stops: The Special Effects
There were several special effects in the show- the two larger effects were run with our Creative Conners equipment (the Revolver and the Spotline). We used our smaller stock wheels down turntable (18’ diameter) with luan facing and an MDF deck. We wrapped the outer edge of the turntable with 6” grip tape to create better friction to the Revolver motor drive.
To fly Jane Doe, we special ordered a flying harness from ZFX that fit our actor, and used the creative Connors spotline motor to run the effect. Several weeks before load-in, I went to the Met theatre to take measurements of the grid above the stage in order to custom design seave frames that would drop the wire rope in the exact spot. We used J bolts to attach the sheave frames to the grid and ran wire rope from the spotline drum, up to the grid, over and down above Jane Doe’s flight path.
We tested the flight several times with sandbags before testing with humans. Once we blocked out the track of the flight, we fitted the harness to the actor and set aside time during tech to rehearse the entire flight (from hookup to release) with the director, stage manager, as well as the actors and stage crew involved with the effect. In any automated effect, It is vital that the automation operator has a direct line of sight to the actor and the effect, as they are watching for specific signals from all involved during the flight, and can quickly prevent a dangerous situation should something go wrong at any point.
Seeing the Final Product:
Watching the show opening night was nothing less than cathartic to me. The actors gave a phenomenal performance, and I was filled with pride for the tech crew and everyone involved in pulling off this technical marvel. I am so happy to be able to leave this program with such a successful production, and having learned so much along the way.
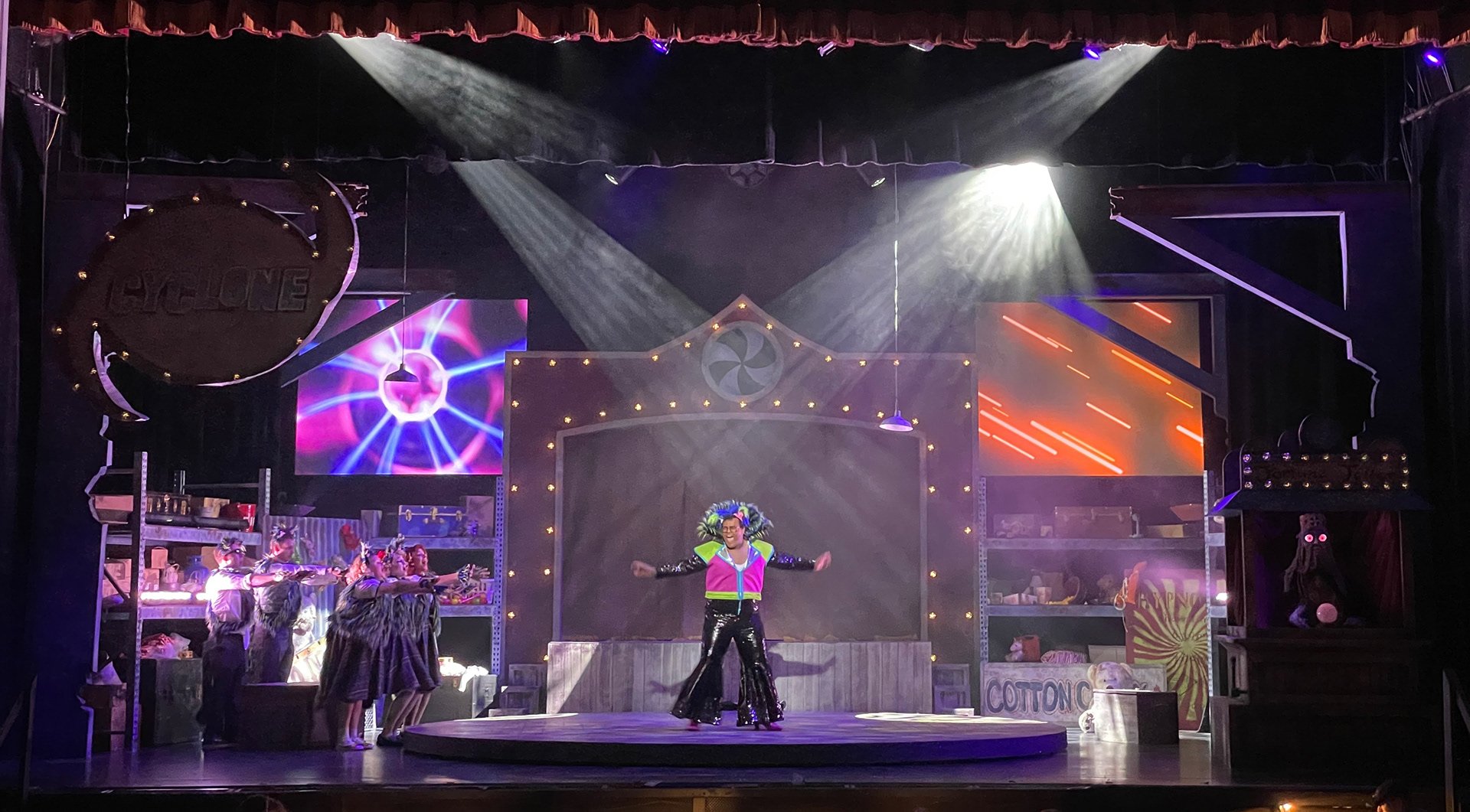